各検証試験結果・品質管理体制
エコザックの各種試験
エコザックの接合耐力
ZAM® t =2.3mm、3.2mmとシュアツイストの接合耐力
基準耐力 kN
SB1250DB
引 張 | せん断 | |
---|---|---|
t=2.3mm | 2.85 | 10.55 |
t=3.2mm | 5.37 | 15.10 |
短期許容耐力=基準耐力 長期許容耐力=短期許容耐力×1/1.5
耐緩み試験
付トルク30N・mでシュアツイストとM10・M12ボルトナットの戻しトルクを比較
締付トルク(N・m) | 戻しトルク(N・m) | |
---|---|---|
シュアツイスト SB1250DB |
30.0 | 20.5 |
M12×1.75(並目) バネ座金使用 |
30.0 | 22.6 |
M10×1.5(並目) バネ座金使用 |
30.0 | 20.2 |
シュアツイストの耐緩み性はボルトナットと同等
振動試験
- 自動車部品振動試験方法(JIS D 1601)
- 振動数33Hz 振幅3mm 負荷荷重5kg 振動加速度6.6G
17時間(200万回)の加振で緩みなし
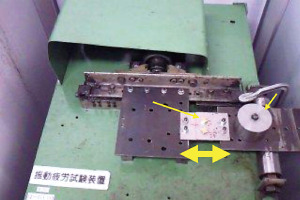
電磁式疲労試験機
実物大試験
三点曲げ試験
風荷重に対して接合部の安全性を確認
- 胴縁本体の終局耐力に対して接合部の損傷無し
- 胴縁中央部の変位17.23mmに対して、接合部の変位量1mm以下
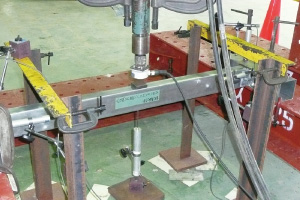
三点曲げ試験
層間変位試験
水平荷重に対する層間変形角 1/120以下に対して安全性を確認
- 胴縁本体の終局層間変位180mm(1/10)に対して損傷無し
- 接合部の変位量1mm以下
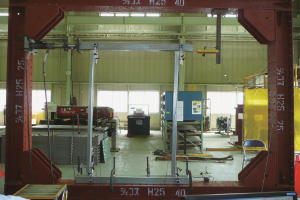
層間変位試験
耐食性試験
シュアツイストと高耐食めっき鋼板および溶融亜鉛めっきの組み合わせによる耐食性試験
- 中性塩水噴霧サイクル試験(JIS H 8502)
- 1サイクル(8時間)=塩水噴霧2時間+乾燥4時間+湿潤2時間
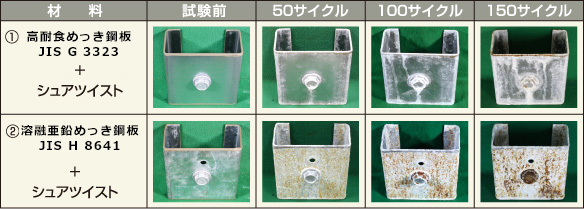
*形鋼サイズ:C100×50×20×t2.3mm、①K14、②HDZ40、シュアツイスト:SB1250DB
接合部詳細図
接合部材として、
工場:角型鋼管(100×100×3.2)
現場:リップ溝型鋼(100×50×20×3.2)
ネコピース:(L50×50×3.2×90)の場合を示す。
工場:角型鋼管(100×100×3.2)
現場:リップ溝型鋼(100×50×20×3.2)
ネコピース:(L50×50×3.2×90)の場合を示す。
※狭小部位には、溶接接合を選択する場合があります。
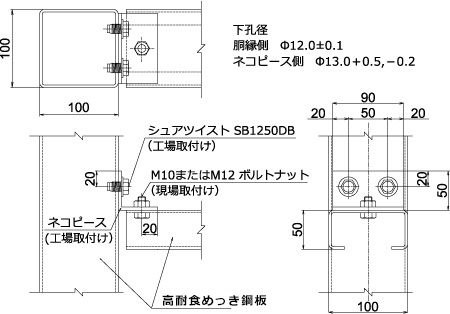
品質管理体制
認定制度
エコザック普及協議会(以下、本協議会)が開催する技術講習会を受講し、適切に認定性としています(定期的に監査も実施)。
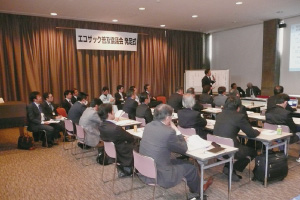
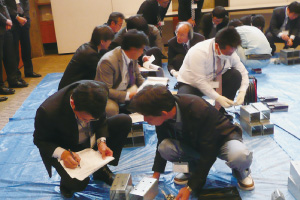
技術講習会(座学、実技の2部構成)
品質管理内容
下表のように製造時に締付トルクや胴縁の下穴径、板厚等を適宜確認し、記録に残すことで確実な品質管理が行える体制としています。
また、製造方法と品質管理方法を記録したDVD「エコザック製造手順」を正会員に配布し周知を図っています。
項 目 | 検査対象 | 確認内容 | 頻 度 |
---|---|---|---|
1)使用前検査 | ・鋼管、型鋼 | ・サイズ、検査証明書と荷札の照合、板厚 | 作業日毎に1回 |
・シュアツイスト | ・形式、検査報告書No、ロットNo、ねじ山径等 | ||
・ネコピース | ・寸法、形状、外観、挿入孔径 | ||
2)作業前確認 | ・試験材の板厚、孔径確認 | ・下孔径、板厚測定 | 作業日毎または 作業班毎に1回 |
・インパクトレンチのトルク設定 | ・トルク目安t2.3:約30N・m、t3.2:約50N・m | ||
・シュアツイスト4本を締結し、 締付け後のトルクを測定する。 |
・規定のトルク範囲内か確認する。 ・t2.3:26~53N・m、t3.2:40~78N・m |
||
3)製造中の抜取検査 | ・製造途中の不具合有無確認のため、 各寸法、締付け後のトルクを測定 |
・シュアツイスト外形 | 午前、午後に 各1回以上 |
・板厚、下穴径 | |||
・追締めトルク | |||
4)製造後の検査 | ・着座の確認 | ・目視にて全数確認 | 製造後に1回 |
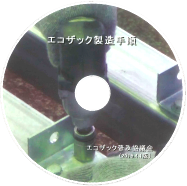
DVD「エコザック製造手順」の内容(約30分)
- 1. 工具、検査機器について
- 2. 製造記録の記入内容
- 3. 被締結材の使用前検査方法
- 4. 被締結材の穴あけ作業
- 5. 専用工具の調整作業
- 6. 製造
- 7. 製造中の抜き取り検査方法
- 8. 製造後の検査方法
- 9. ねじ切れ時の対処方法
- 10. 白錆発生時の対処方法
- 11. アトラーによる穴あけ作業
不具合対応
正会員各社で製造時または施工後に不具合があった場合は、正会員各社で応急対応すると共に、その情報を本協議会に報告し、対応を協議、その結果を正会員各社(全社)に連絡する体制としています。
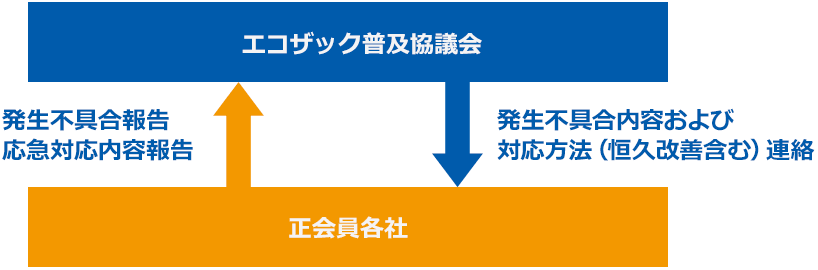